Defoamers and Their Impact on Reducing Foam in Liquid Systems
Defoamers and Their Impact on Reducing Foam in Liquid Systems
Blog Article
The Duty of Defoamers in Enhancing Product High Quality and Efficiency
In different producing processes, the presence of foam can considerably hinder item high quality and functional performance. Defoamers function as vital additives that alleviate this concern, making certain smoother production workflows while enhancing the functional and visual attributes of the end products (defoamers). Their application extends a plethora of markets, from food and drink to drugs, where consistency and dependability are paramount. However, the choice of the ideal defoamer can be critical to accomplishing optimal outcomes, increasing crucial concerns concerning formulation compatibility and performance metrics that warrant further expedition.
Comprehending Defoamers
Comprehending the function of defoamers is necessary for maintaining product top quality across different industries. Defoamers are chemical additives created to minimize and stop the formation of foam in liquid systems, which can detrimentally impact procedures such as mixing, filling up, and surface tension. Frothing can bring about inadequacies, item issues, and compromised aesthetic appeal, making defoamers a vital element in manufacturing operations.
In commercial applications, defoamers aid to enhance product uniformity and stability. The effective usage of defoamers not only guarantees smoother production processes but additionally contributes to superior item efficiency.
Additionally, the option and formula of a defoamer should line up with details application needs, such as compatibility with other components, effectiveness under differing temperature and pH conditions, and possible regulatory constraints. Eventually, understanding defoamers' features and their significance in different formulations is crucial for enhancing production and making sure the greatest top quality output.
Types of Defoamers
Defoamers can be categorized into several kinds based on their composition and system of action. The key kinds consist of silicone-based, non-silicone organic, and not natural defoamers.
Silicone-based defoamers are amongst one of the most reliable, mostly because of their capacity to spread out quickly on the fluid surface area and interfere with foam development. Their distinct chemical framework permits for superior stability, making them suitable for high-temperature applications and settings with differing pH levels.
Non-silicone organic defoamers, typically composed of all-natural oils or fatty acids, are valued for their biodegradability and lower toxicity. These are normally utilized in food and beverage applications where safety and ecological effect are extremely important.
Not natural defoamers, that include substances like talc or calcium carbonate, act by increasing the thickness of the liquid, therefore lowering foam stability. They are frequently used in commercial processes where compatibility with various other materials is not a problem.
Each sort of defoamer has unique benefits and limitations, enabling customized remedies depending upon the particular frothing concerns come across in different applications. Recognizing these distinctions is essential for maximizing performance and accomplishing desired product high quality.
Applications Throughout Industries
Various markets leverage defoamers to improve item top quality and functional effectiveness. In the food and beverage sector, defoamers are vital in processes such as brewing and dairy products manufacturing to avoid foam development, which can result in inefficiencies and item disparity. By managing foam, suppliers can make sure better yield and an extra uniform item.
In the pharmaceutical market, defoamers play a vital duty in the formula of liquid medications, where extreme foam can hinder blending and precise dosing. Their use helps keep the integrity of the formulas and facilitates smoother production procedures.
The paint and layers sector additionally depends on defoamers to boost the efficiency of products throughout application. By lessening foam, these additives make sure a smoother coating and improve the visual top qualities of the end product.
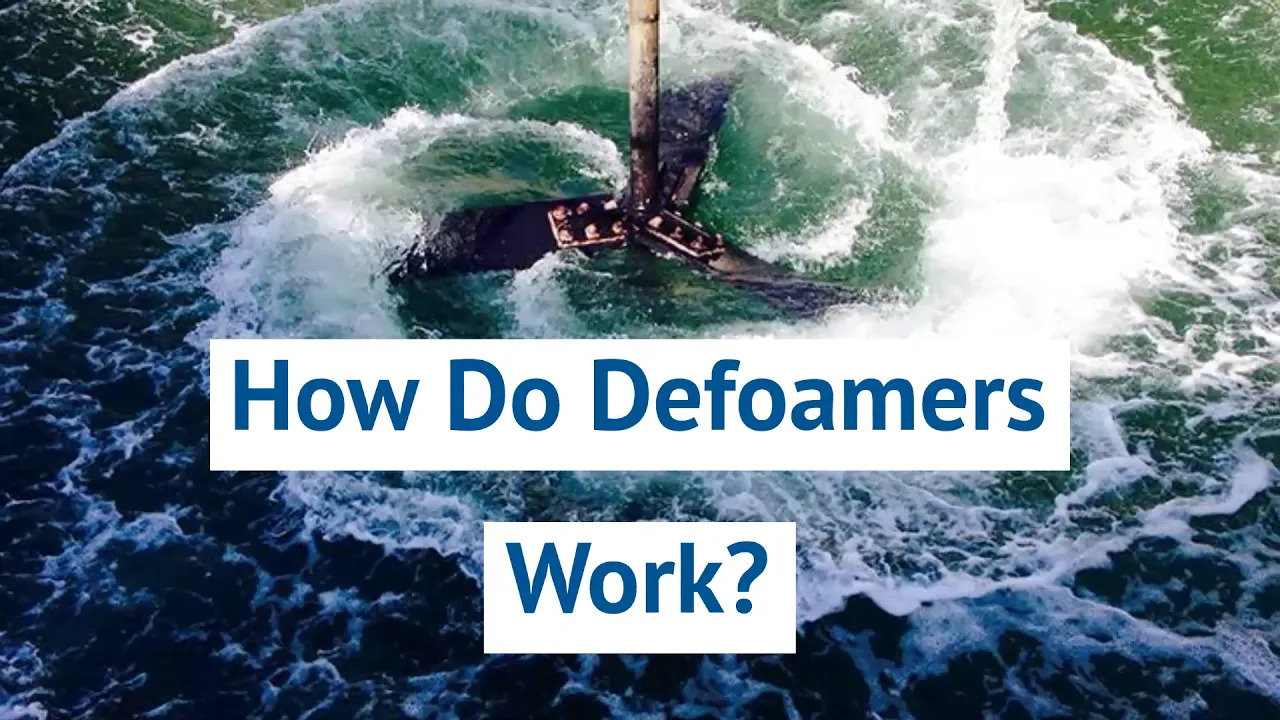
Advantages of Using Defoamers
While the application of defoamers varies throughout markets, their benefits consistently improve product top quality and process effectiveness. One significant benefit is the reduction of foam formation throughout making procedures, which can otherwise cause production hold-ups and inconsistencies in item high quality. By reducing foam, defoamers make it possible for a smoother flow of materials, helping with more efficient procedures and decreasing the chance of devices malfunctions.
In addition, the use of defoamers can enhance the appearance and texture anonymous of end products. In fields such as coatings, paints, and food processing, excessive foam can jeopardize the aesthetic aesthetics and general high quality, while the proper defoamer application makes sure go to website an uniform surface and desirable features. Furthermore, defoamers can add to cost financial savings by reducing waste during manufacturing and maximizing the use of raw products (defoamers).

Picking the Right Defoamer
Choosing the best defoamer is essential for maximizing production procedures and guaranteeing item high quality. The selection of defoamer affects not just the performance of foam control however likewise the general performance characteristics of the end product. Variables to take into consideration consist of the kind of application, the chemistry of the formulation, and the ecological problems under which the product will be utilized.
Different industries might need particular defoamer kinds, such as silicone-based, natural, or polymeric defoamers. Recognizing the compatibility of the defoamer with the main components is vital to prevent negative responses that can endanger product stability. Furthermore, the defoamer's efficiency in numerous temperature levels and pH degrees have to be assessed to make certain constant efficiency.
Testing the defoamer in small-scale applications can supply beneficial understandings into its performance and suitability. Factor to consider of governing conformity, particularly in food, pharmaceuticals, and cosmetics, is extremely important in selecting a defoamer. Eventually, a detailed assessment of these factors will cause the selection of a defoamer that not just regulates foam properly but additionally enhances the quality and performance of the end product.
Final Thought

In conclusion, defoamers are vital additives that dramatically boost product top quality and performance throughout explanation numerous industries. By effectively reducing foam formation, these representatives not only improve functional efficiency but also add to the useful and visual integrity of items. The strategic option and application of defoamers cause set you back financial savings, optimized resource usage, and boosted consumer fulfillment. Overall, the importance of defoamers in industrial processes can not be overemphasized, as they play an essential function in achieving constant and top notch outcomes.
Frothing can lead to inadequacies, product flaws, and compromised visual charm, making defoamers a crucial element in producing procedures.

Report this page